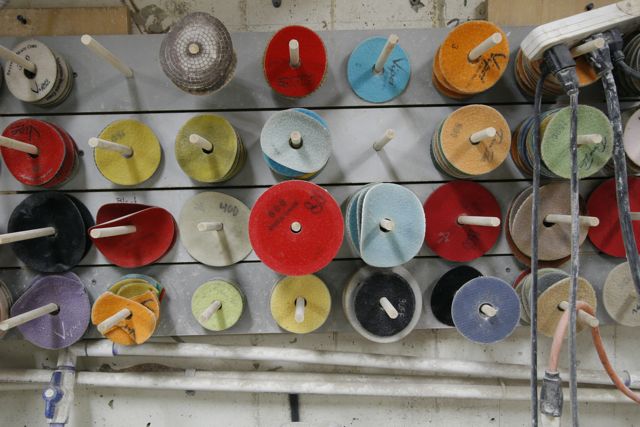
The discs used by the robo-polisher in successive steps from coarse to ultra-fine in order to make a smooth glass countertop.
The kitchen is nearing completion and one of the final components is the countertop that will be installed on the cabinets. We have selected a material, “recycled glass”, to provide this important work surface. As one might expect, it comprises glass fragments from recycled glass containers, selected from various sources and mixed to obtain a particular color and texture appearance, and then sealed within a binder. Some manufacturers use a concrete binder. Our supplier, Rust Brothers, uses a class of epoxy having no volatiles (fumes).
Despite the source being recycled stuff, the material is fairly expensive, and the crafting and polishing adds to the total cost. We wanted to make sure it will look and perform to the level expected of this expense, which is comparable to granite, quartz, and other engineered stone materials. We ordered a sample of it to see it in the lighting and context of This Odd Kitchen alongside the Ikea cabinet and flooring colors. We also conducted a customized stain test by applying the most likely things to spill on it: coffee, wine, and hot sauce (it passed!).
There is a tricky orchestration that must happen to end up with a countertop that fits precisely, especially in a kitchen built around non-square walls. The edges and features need to align, and the openings for sinks must be carefully created. Before the slabs of material could be cast, an exact template of the countertops and walls had to be made. Troy, one of the Rust Brothers (they aren’t really brothers) came out to build a template from strips of hardboard and hot glue. Where the walls curved and waved, he carefully carved the template to match. The angles and notches were set and cut to exactly mate with the features of the kitchen and cabinets. He took the template back to the shop to be used in cutting and grinding the raw slabs that would be cast.
They refused to cut the hole for the sink from the manufacturers specifications; I think they had been burned before. They needed the actual physical sink before committing to that step, so that meant I needed to decide on one, obtain it, and deliver it to their shop. It stressed me to think about this important aspect of the kitchen, but to avoid holding things up, I made a selection, and the eventual sink delivery turned out to be a great field trip!
We met Brady, one of the owners (still not a brother) who showed us where the material was cast, and how it was shaped and polished. We saw our actual countertop sections, already polished, waiting for the final cutting. Brady was an articulate and skilled artisan, someone who had developed sources of raw supplies beyond just glass, including walnut shells, cork, mother of pearl, and laminated paper, and had devised innovative methods and controls to make them into beautiful and useful materials. He was justifiably proud of the techniques and the products that they created.
It was a pleasure to have him show his equipment and facilities to us. Here are some of the photos of the place.
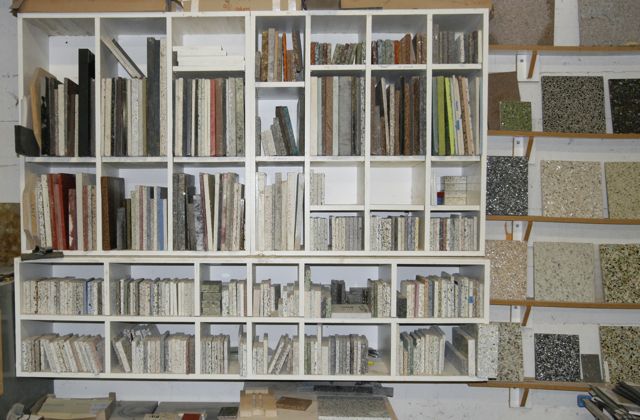
A sampling of the many items that Rust Brothers converts into countertops and other interior materials.
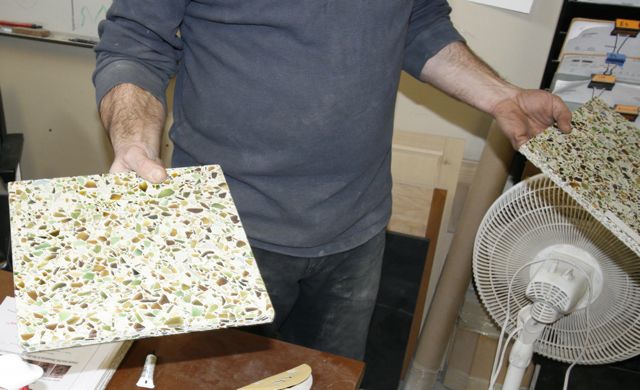
The “Hennepin” style of recycled glass. The material comes from the recycled glass of Hennepin county, and the mix ratio between brown (beer) and green (wine) glass, changes with the seasons!
I am relieved to know that you did the necessary endurance testing before choosing this counter top. I wasn’t as thorough, with my only criteria being recycled products and the color choices. Yes, I have learned that using recycled products is more expensive and more time consuming. Thanks for sharing this, and Happy New Year! Tina